Welding Material Selection Guide: Choosing the Right Supplies for Your Industrial Project
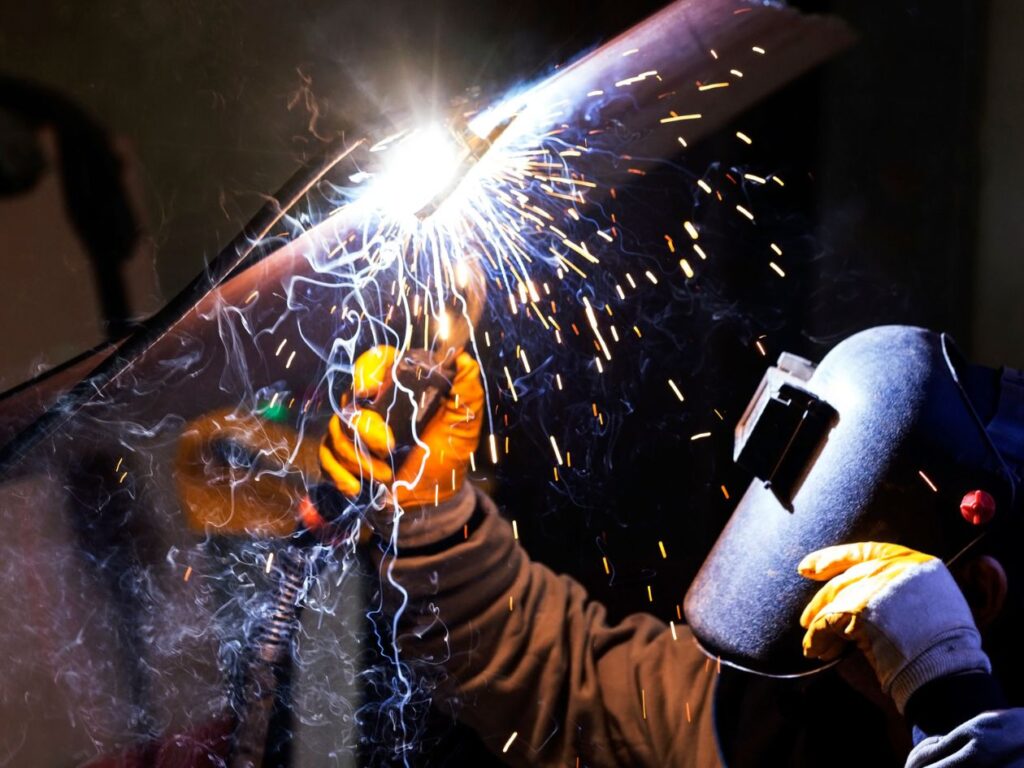
Selecting the right welding materials is crucial for achieving strong, durable joints that meet the demanding requirements of industrial applications. Whether you’re working in manufacturing, automotive, oil and gas, or general fabrication, the success of your welding projects depends on choosing materials that match your specific application requirements, environmental conditions, and performance standards.
This comprehensive guide will help you navigate the complex world of welding materials and make informed decisions for your industrial projects. Proper material selection can significantly impact project outcomes, operational costs, and long-term performance.
Understanding Base Material Properties
The foundation of proper welding material selection begins with a thorough understanding of your base materials. Different metals require specific welding approaches and compatible filler materials to achieve optimal results.
Carbon Steel Applications Carbon steel remains the most common material in industrial welding applications due to its versatility and cost-effectiveness. Low-carbon steels (mild steel) are generally easy to weld and work well with a variety of welding processes. Medium and high-carbon steels require more careful heat management and may need preheating or post-weld heat treatment to prevent cracking.
Stainless Steel Considerations Stainless steel welding requires careful attention to maintaining corrosion resistance while achieving strong mechanical properties. The chromium content that gives stainless steel its corrosion resistance can be depleted during welding, making proper filler metal selection and welding technique critical for maintaining performance.
Aluminum and Its Alloys Aluminum welding presents unique challenges due to the material’s high thermal conductivity and tendency to form oxide layers. Proper cleaning, appropriate filler metal selection, and controlled atmospheric conditions are essential for successful aluminum welding in industrial applications.
Welding Process Selection and Material Compatibility
Your choice of welding process directly influences material selection and ultimately affects weld quality, productivity, and cost-effectiveness.
Gas Metal Arc Welding (GMAW/MIG) GMAW offers excellent productivity for manufacturing and fabrication applications. The continuous wire feed allows for faster welding speeds, making it ideal for production environments. Shielding gas selection is crucial, with argon-based mixtures typically used for non-ferrous metals and CO2 or argon-CO2 mixtures for carbon steel applications.
Gas Tungsten Arc Welding (GTAW/TIG) GTAW provides superior control and weld quality, making it the preferred choice for critical applications in aerospace, food processing, and pharmaceutical industries. The process allows for precise heat input control and produces high-quality welds with excellent mechanical properties.
Shielded Metal Arc Welding (SMAW/Stick) SMAW remains popular for field welding and repair work due to its portability and versatility. Electrode selection is critical, with different coatings designed for specific applications, positions, and base materials.
Flux-Cored Arc Welding (FCAW) FCAW combines the productivity of GMAW with the versatility of SMAW, making it excellent for structural welding and heavy fabrication. The flux core provides internal shielding and can include alloying elements to enhance weld properties.
Filler Metal Selection Criteria
Choosing the right filler metal is one of the most critical decisions in welding material selection. The filler metal must be compatible with the base material while providing the necessary mechanical properties for the intended application.
Matching Base Material Properties The filler metal should closely match the base material’s chemical composition and mechanical properties. For structural applications, the filler metal must meet or exceed the base material’s strength requirements while maintaining adequate ductility and toughness.
Environmental Considerations Consider the operating environment when selecting filler metals. Corrosive environments may require stainless steel or nickel-based filler metals, while high-temperature applications might need specialized high-temperature alloys.
Welding Position Requirements Different welding positions require filler metals with specific characteristics. Vertical and overhead welding typically requires filler metals with faster freezing characteristics to prevent sagging and ensure proper penetration.
Shielding Gas Selection for Optimal Results
Proper shielding gas selection protects the weld pool from atmospheric contamination while influencing arc characteristics, penetration, and overall weld quality.
Argon-Based Mixtures Pure argon provides excellent arc stability and is typically used for aluminum and stainless steel welding. Argon-helium mixtures increase heat input and are beneficial for thicker materials or when higher welding speeds are required.
Carbon Dioxide and Mixed Gases CO2 provides deep penetration and is cost-effective for carbon steel welding, though it can produce more spatter. Argon-CO2 mixtures offer a balance between penetration, arc stability, and cost-effectiveness for general steel welding applications.
Specialized Gas Mixtures Some applications require specialized gas mixtures to achieve specific weld characteristics. These might include nitrogen additions for duplex stainless steels or oxygen additions for improved arc stability in certain applications.
Quality Standards and Code Requirements
Industrial welding applications must comply with various codes and standards that specify material requirements, testing procedures, and acceptance criteria.
AWS (American Welding Society) Standards AWS standards provide comprehensive guidelines for welding procedures, filler metal classifications, and quality requirements. Understanding these standards is essential for selecting appropriate materials and ensuring compliance.
ASME and API Codes Pressure vessel and piping applications must comply with ASME and API codes that specify material requirements, welding procedures, and testing protocols. These codes often require specific filler metals and welding procedures to ensure safe operation.
Industry-Specific Requirements Different industries have specific requirements that influence material selection. Automotive applications may require specific strength levels, while food processing applications need materials that maintain sanitary conditions.
Cost Optimization Strategies
Balancing performance requirements with cost considerations is essential for successful industrial welding projects.
Material Utilization Efficiency Proper material selection can reduce waste and improve productivity. Choosing filler metals with appropriate deposition rates and minimal cleanup requirements can significantly impact overall project costs.
Inventory Management Maintaining optimal inventory levels of welding materials reduces carrying costs while ensuring availability when needed. Consider working with suppliers who offer custom procurement services to optimize your welding material inventory.
Long-Term Performance Considerations While initial material costs are important, consider the long-term performance and maintenance requirements. Higher-quality materials may have higher upfront costs but can provide better long-term value through reduced maintenance and longer service life.
Common Material Selection Challenges
Understanding common challenges in welding material selection helps prevent costly mistakes and ensures successful project outcomes.
Dissimilar Metal Joining Joining dissimilar metals requires careful consideration of thermal expansion differences, galvanic corrosion potential, and mechanical property variations. Specialized filler metals or transition joints may be necessary.
Contamination Prevention Contamination from oil, paint, or other surface contaminants can significantly impact weld quality. Proper cleaning procedures and material storage are essential for maintaining weld integrity.
Heat Input Management Excessive heat input can cause distortion, reduce mechanical properties, or affect corrosion resistance. Proper material selection and welding procedures help manage heat input effectively.
Quality Assurance and Testing
Implementing proper quality assurance procedures ensures that welding materials perform as expected in service.
Non-Destructive Testing Regular inspection using appropriate non-destructive testing methods helps identify potential issues before they become problems. This includes visual inspection, dye penetrant testing, and radiographic inspection as appropriate.
Mechanical Testing Periodic mechanical testing of welded joints ensures that materials are performing as expected and meeting code requirements. This may include tensile testing, bend testing, and impact testing.
Documentation and Traceability Maintaining proper documentation of materials used, welding procedures, and inspection results provides traceability and supports quality assurance efforts.
Technical Support and Expert Guidance
Navigating the complexities of welding material selection can be challenging. Working with experienced suppliers and technical experts can provide valuable insights into material choices for specific applications.
Technical expertise should cover all aspects of welding material selection, from base material compatibility to code compliance requirements. Look for suppliers who can understand your specific needs and recommend materials that optimize both performance and cost-effectiveness.
Achieving Success in Industrial Welding Projects
Successful welding material selection requires careful consideration of multiple factors, including base materials, welding processes, environmental conditions, and code requirements. By understanding these factors and working with experienced suppliers, you can ensure that your welding projects meet performance requirements while optimizing costs and productivity.
The key to successful welding material selection lies in understanding the specific requirements of your application and choosing materials that provide the best combination of performance, quality, and cost-effectiveness. This requires expertise, experience, and access to high-quality materials from trusted suppliers.
Proper material selection, combined with skilled welding techniques and appropriate quality control measures, forms the foundation for reliable, long-lasting welds that meet the demanding requirements of industrial applications.
For expert guidance on welding material selection and access to professional-grade welding supplies, contact Cruco Supply and Industry. Our team can help you navigate the complexities of material selection to ensure your industrial welding projects achieve optimal results.