Cost-Saving Strategies for Small Machine Shops: Tools and Techniques
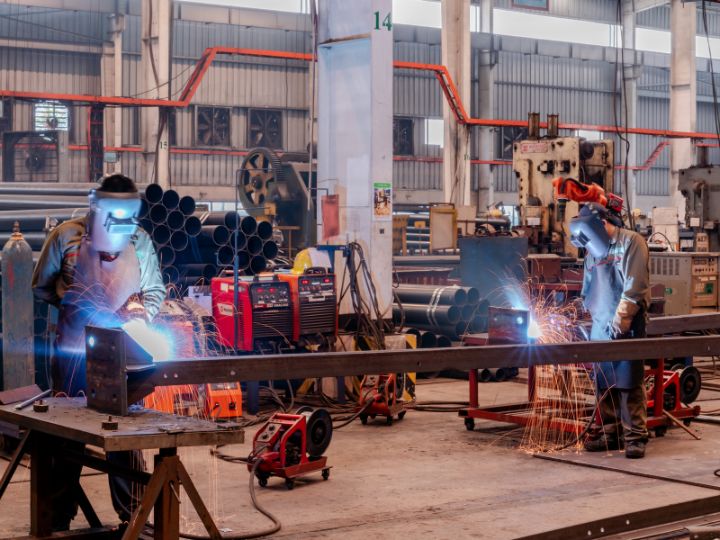
In today’s competitive manufacturing landscape, small machine shops face unique challenges. Operating with tighter budgets, smaller teams, and often less specialized equipment than larger competitors, these businesses must maximize efficiency while minimizing costs to remain profitable. This comprehensive guide explores practical, implementable strategies that can help small machine shops reduce expenses without sacrificing quality or productivity.
Understanding Your Current Costs
Before implementing cost-saving measures, it’s essential to have a clear picture of where your money is currently going.
Conduct a Comprehensive Cost Analysis
1. Break Down Direct Costs
- Material costs per job
- Labor hours and rates
- Tooling consumption
- Machine operating costs (power, coolant, etc.)
2. Identify Indirect Costs
- Facility overhead (rent, utilities, insurance)
- Administrative expenses
- Maintenance and downtime
- Quality control and inspection
- Waste disposal and environmental compliance
3. Calculate True Job Costs
- Develop accurate job costing methods
- Track setup time vs. production time
- Account for machine depreciation
- Include programming and preparation time
4. Identify Cost Trends
- Track costs over time to identify increases
- Compare costs against industry benchmarks
- Analyze seasonal variations
- Note which jobs consistently generate the highest margins
Optimizing Material Usage
Materials often represent 40-60% of total job costs for machine shops. Minimizing waste and maximizing material efficiency can dramatically improve profitability.
Material Selection and Purchasing Strategies
1. Strategic Buying Practices
- Consolidate orders to qualify for volume discounts
- Develop relationships with key suppliers for better pricing
- Consider joining buying cooperatives with other small shops
- Negotiate consignment arrangements for commonly used materials
2. Inventory Management
- Implement just-in-time practices where appropriate
- Use inventory management software to optimize stock levels
- Consider vendor-managed inventory for high-volume materials
- Track material usage to identify waste sources
3. Alternative Materials
- Regularly evaluate new material options
- Consider near-net-shape stock to reduce machining time
- Look for multi-certified materials that can serve multiple applications
- Investigate material substitutions that maintain performance at lower cost
Reducing Material Waste
1. Optimize Nesting and Cut Planning
- Use nesting software to maximize material yield
- Plan cuts to minimize drops and unusable pieces
- Maintain a database of remnants and drops for future use
- Consider standardizing material sizes where possible
2. Recycle and Repurpose
- Implement systematic recycling of chips and scrap
- Segregate metal types for maximum recycling value
- Track scrap rates by job and operator to identify improvement opportunities
- Find creative uses for drops (fixtures, small parts, etc.)
3. Optimize Programming for Material Efficiency
- Program tool paths to minimize material removal
- Use simulation software to verify programs before cutting material
- Consider roughing strategies that minimize cutting forces and tool wear
- Evaluate the true cost-benefit of tighter tolerances that require more material
Tooling Optimization
Cutting tools represent a significant ongoing expense. Strategic tool management can reduce costs while improving performance.
Tool Selection and Management
1. Tool Standardization
- Reduce variety of specialized tools when possible
- Standardize on versatile tool geometries
- Create a approved tool list to prevent unnecessary purchases
- Develop standard tool packages for common operations
2. Tool Life Optimization
- Track tool life and performance data
- Test and optimize cutting parameters
- Implement progressive tool wear compensation
- Establish clear tool replacement criteria
3. Tool Inventory Control
- Implement tool crib management systems
- Use vending systems for high-value tools
- Create optimal reorder points based on usage
- Conduct regular tool audits
Cost-Effective Tool Strategies
1. Tool Reconditioning
- Establish in-house resharpening capabilities where economical
- Develop relationships with quality tool regrinding services
- Analyze cost-benefit of regrinding vs. replacement
- Consider modular tooling systems with replaceable inserts
2. Strategic Tool Investment
- Evaluate premium tools based on total cost per part
- Calculate true cost including reduced cycle time and longer life
- Test before making large investments
- Consider performance-based agreements with tool suppliers
3. Application-Specific Solutions
- Use the right tool for the job rather than general-purpose tools
- Consider special tools for high-volume work
- Evaluate custom tool solutions for problem applications
- Balance inventory costs against performance benefits
Technology and Automation Solutions
1. Strategic Automation for Small Shops
- Identify low-hanging fruit for automation
- Consider robotic loading/unloading
- Evaluate bar feeders and parts catchers
- Implement pallet systems for unattended operation
2. Lights-Out Manufacturing Approaches
- Start with simple, repeatable processes
- Develop robust error detection and recovery
- Implement remote monitoring capabilities
- Begin with partial lights-out (extended shifts)
3. Process Monitoring and Optimization
- Use machine monitoring systems to track utilization
- Implement tool monitoring to prevent scrap
- Track overall equipment effectiveness (OEE)
- Use data to identify improvement opportunities
Equipment and Technology Investment Strategies
Strategic investment in the right equipment can reduce costs long-term, but requires careful analysis.
Equipment Acquisition Approaches
1. New vs. Used Equipment Evaluation
- Calculate total cost of ownership, not just purchase price
- Consider energy efficiency in operating costs
- Factor in reliability and maintenance requirements
- Evaluate parts availability and technical support
2. Financing and Tax Strategies
- Explore Section 179 deductions and bonus depreciation
- Compare leasing vs. purchasing options
- Investigate equipment financing programs
- Consider equipment sharing arrangements with complementary businesses
3. Retrofit and Upgrade Options
- Evaluate control system upgrades for older machines
- Consider spindle rebuilds and mechanical refurbishment
- Implement monitoring systems on existing equipment
- Add automation to manual machines where feasible
Technology Implementation
1. Software Solutions
- Implement ERP/MRP systems scaled for small shops
- Use CAM software to optimize programming
- Consider cloud-based solutions to reduce IT overhead
- Explore shop management software with mobile capabilities
2. Quality and Measurement Technology
- Evaluate in-process measurement systems
- Consider entry-level CMM or vision systems
- Implement statistical process control (SPC)
- Use tool presetters to reduce setup time and improve accuracy
3. Digital Transformation Strategies
- Start with digital job travelers
- Implement barcode scanning for inventory and job tracking
- Consider digital work instructions
- Leverage IoT sensors for condition monitoring
Creating Your Cost-Saving Roadmap
Cost reduction for small machine shops isn’t a one-time initiative but rather an ongoing strategic approach. The most successful shops combine immediate tactical improvements with long-term strategic changes in how they operate.
Begin by understanding your true costs, then prioritize initiatives based on potential impact and ease of implementation. Start with quick wins to build momentum, then tackle more significant structural changes that create lasting competitive advantage.
Remember that cost-saving isn’t just about cutting expenses—it’s about creating a more efficient, productive, and profitable operation. The most effective cost reductions often come from eliminating waste rather than reducing capabilities.
By implementing a comprehensive approach that addresses materials, tooling, labor, energy, equipment, maintenance, quality, administration, training, and marketing, small machine shops can dramatically improve profitability while enhancing their ability to compete in increasingly challenging markets.
Take Your Small Machine Shop to the Next Level with Cruco Mill & Industry Supply
At Cruco Mill & Industry Supply, we understand the unique challenges facing small machine shops. For over 30 years, we’ve been helping businesses like yours implement practical, cost-effective solutions that drive productivity and profitability.
Our Cost-Saving Partnership Programs include:
- Tooling Optimization Services: Our technical specialists will analyze your current tooling usage and recommend standardization and optimization strategies that reduce costs while improving performance.
- Inventory Management Solutions: From vendor-managed inventory to customized tool cribs, we offer tailored solutions that reduce carrying costs while ensuring you always have what you need.
- Technical Training and Support: Take advantage of our expertise through hands-on training programs, technical seminars, and application support that helps you get the most from your tooling investment.
- Cost Analysis Consultation: Our team can help you identify hidden costs in your operation and develop practical strategies for reducing them without compromising quality or capacity.
- Premium Products at Competitive Prices: Access to industry-leading brands and specialized tooling solutions at prices that work for small shops, with quantity discounts tailored to your actual usage patterns.
Don’t waste valuable time and resources on trial-and-error approaches to cost reduction. Partner with Cruco Mill & Industry Supply for expert guidance and proven solutions tailored to your specific needs.Visit https://crucosupply.com/ to schedule your free cost-saving consultation. Let us help you cut costs, not corners, and build a more profitable machine shop operation!