5 Essential Power Tool Maintenance Tips That Will Save Your Business Thousands
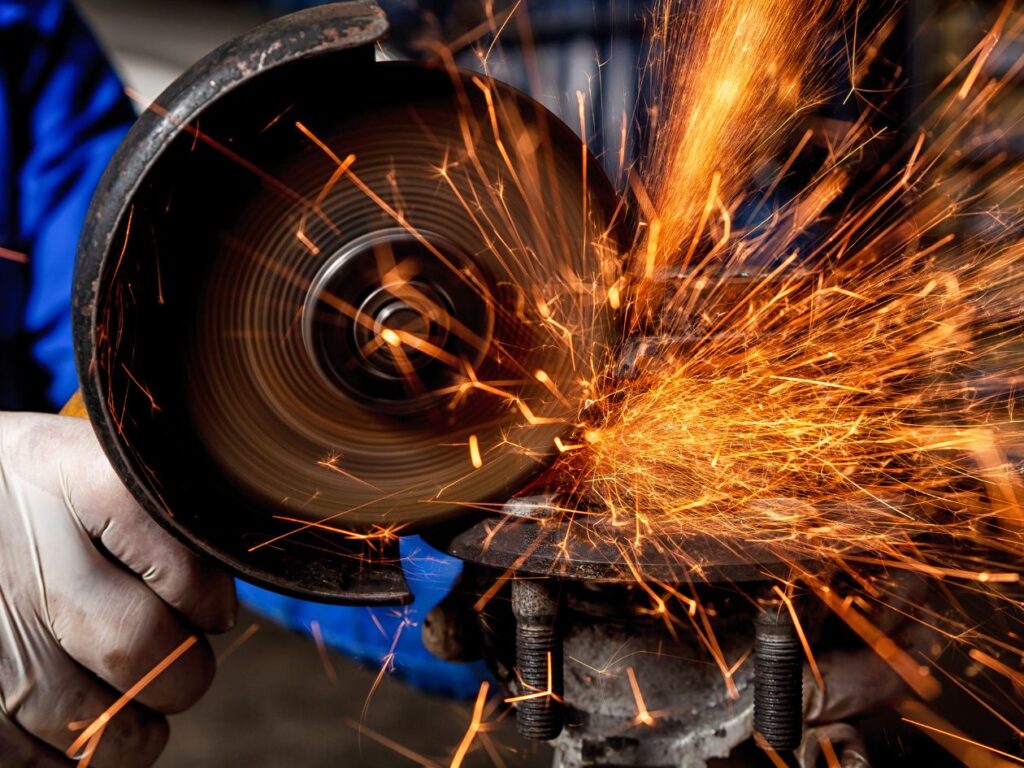
Power tools are the backbone of any manufacturing operation, fabrication shop, or industrial facility. At Cruco Mill & Industrial Supply, we’ve seen firsthand how proper maintenance can extend tool life from months to years, while poor maintenance practices can turn a $500 tool into scrap metal overnight. After two decades of serving North Carolina’s industrial community, we’ve identified five critical maintenance practices that can save your business thousands of dollars in replacement costs and lost productivity.
The Hidden Cost of Poor Tool Maintenance
Before diving into our maintenance tips, consider the true cost of tool failure. A failed grinder doesn’t just cost $300 to replace—it costs worker downtime, project delays, emergency procurement fees, and potentially safety incidents. Industry studies show that businesses practicing proper tool maintenance see 40-60% longer tool life and 25% fewer safety incidents compared to those with poor maintenance habits.
Tip #1: Implement a Daily Cleaning Regiment
Why It Matters Dust, metal shavings, and debris are power tools’ worst enemies. They infiltrate moving parts, clog ventilation systems, and create abrasive conditions that accelerate wear. A simple daily cleaning routine can prevent 80% of premature tool failures.
Best Practices Start each shift with a quick visual inspection and end with a thorough cleaning. Use compressed air to blow out dust and debris from motor vents, chuck mechanisms, and gear housings. For tools used in wet environments, ensure complete drying before storage to prevent corrosion.
Special Attention Areas
- Motor ventilation slots
- Chuck and bit-holding mechanisms
- Cord connections and strain reliefs
- Battery terminals and charging ports
- Trigger mechanisms and safety switches
Pro Tip from Cruco Mill Keep cleaning supplies at each workstation. We recommend soft brushes, compressed air, and appropriate solvents for different applications. Milwaukee tools, which we stock extensively, include specific cleaning recommendations in their manuals that can dramatically extend tool life.
Tip #2: Master Proper Lubrication Techniques
Understanding Lubrication Needs Different tools require different lubrication schedules and products. Pneumatic tools need daily oiling, while electric tools may require periodic gear grease replacement. Using the wrong lubricant can be worse than no lubrication at all.
Lubrication Schedule Guidelines
- Pneumatic tools: Daily oiling through air line lubricators
- Electric drills/drivers: Monthly chuck lubrication, annual gear service
- Grinders: Bearing lubrication every 100 hours of use
- Hydraulic tools: Weekly hydraulic fluid level checks
Choosing the Right Lubricants Never use automotive oils in pneumatic tools—they can damage seals and valves. Similarly, avoid heavy greases in high-speed applications where they can cause overheating. We stock specialized tool lubricants designed for specific applications.
Red Flags to Watch For
- Unusual noise during operation
- Increased vibration
- Reduced power output
- Overheating during normal use
Tip #3: Perform Regular Electrical System Inspections
Electrical Hazards Are Real Electrical failures account for 30% of power tool accidents and can cause fires, electrocution, or equipment damage. Regular electrical inspections prevent these hazards while identifying problems before they cause failures.
Monthly Electrical Checklist
- Inspect power cords for cuts, kinks, or exposed wires
- Check plug integrity and proper grounding
- Test GFCI protection where required
- Verify switch operation and safety lock functions
- Inspect battery connections and charging systems
Warning Signs of Electrical Problems
- Sparking during operation
- Intermittent power loss
- Unusual heating of cords or plugs
- Flickering lights when starting tools
- Burnt smell during operation
Professional Service Indicators Some electrical issues require professional attention. If you notice consistent tripping of breakers, unusual current draw, or internal arcing, stop using the tool immediately and consult qualified repair technicians.
Tip #4: Maintain Cutting Tools and Accessories
The Multiplier Effect Dull or damaged bits, blades, and accessories don’t just perform poorly—they damage the tools themselves. A dull drill bit creates excessive heat and forces motors to work harder, reducing their lifespan significantly.
Bit and Blade Maintenance
- Keep cutting edges sharp through regular sharpening or replacement
- Store bits properly to prevent damage
- Use appropriate speeds for different materials
- Replace damaged accessories immediately
Heat Management Excessive heat is the enemy of both accessories and tools. Use proper cutting speeds, adequate lubrication, and allow cooling periods during heavy use. Overheated tools experience accelerated wear and potential motor damage.
Inventory Management Maintain adequate supplies of commonly used accessories. Running tools with wrong-sized or damaged bits puts unnecessary stress on motors and drive mechanisms. We help our customers establish proper accessory inventories based on their specific applications.
Tip #5: Establish Preventive Maintenance Schedules
Beyond Daily Care While daily cleaning and inspection are crucial, comprehensive preventive maintenance requires scheduled deeper service. This includes internal cleaning, lubrication, calibration, and replacement of wear items.
Suggested Maintenance Intervals
- Daily: Cleaning, visual inspection, lubrication of pneumatic tools
- Weekly: Detailed inspection of high-use tools, hydraulic fluid checks
- Monthly: Electrical system inspection, battery maintenance
- Quarterly: Internal cleaning, gear lubrication, calibration checks
- Annually: Professional service for critical tools, motor inspection
Documentation Is Key Maintain service records for each tool including purchase date, service history, and performance issues. This data helps predict failures and optimize replacement schedules. Many of our customers use simple logbooks or digital tracking systems.
Training Your Team Ensure all operators understand proper maintenance procedures. A well-trained operator can identify problems early and perform appropriate maintenance. We provide training resources and can recommend local training programs for your team.
Creating a Maintenance Culture
Leadership Commitment Maintenance programs succeed only with management support. Allocate time for proper maintenance and provide necessary supplies and training. The investment in maintenance time pays dividends in reduced downtime and replacement costs.
Incentive Programs Consider implementing programs that reward proper tool care. Some of our customers track tool life by operator and recognize those who consistently achieve above-average performance.
Maintenance Stations Designate specific areas for tool maintenance with appropriate supplies, cleaning equipment, and reference materials. This makes maintenance convenient and more likely to be performed consistently.
The Cruco Mill Advantage
At Cruco Mill & Industrial Supply, we understand that your tools are critical to your operation’s success. Our comprehensive selection of professional-grade Milwaukee tools and accessories is backed by expert technical support and maintenance guidance.
Our Maintenance Support Services
- Technical consultation on proper maintenance procedures
- Recommended maintenance schedules for specific tools
- Supply of appropriate lubricants and cleaning materials
- Training resources and documentation
- Replacement parts and accessories
Professional Repair Network We maintain relationships with qualified repair technicians who can service your tools when professional attention is required. Our network covers everything from simple motor repair to complex hydraulic system rebuilds.
Calculating Your Savings
Implementing these five maintenance practices typically results in:
- 40-60% longer tool life
- 25% reduction in unexpected failures
- 30% decrease in emergency procurement costs
- Improved safety record and reduced insurance claims
- Enhanced productivity through reliable tool performance
For a shop with $10,000 in annual tool purchases, proper maintenance can save $4,000-$6,000 yearly while improving productivity and safety.
Power tool maintenance isn’t just about preventing failures—it’s about maximizing your investment in quality tools while ensuring worker safety and productivity. These five essential practices form the foundation of any successful maintenance program.
Remember that the most expensive tool is the one that fails when you need it most. By implementing daily cleaning, proper lubrication, electrical inspections, accessory maintenance, and preventive scheduling, you’ll keep your tools running reliably while saving thousands in replacement costs.
Your tools are investments in your business’s productivity and profitability. Protect that investment with proper maintenance, and your tools will serve you faithfully for years to come.