The Complete Guide to Choosing the Right Industrial Pipes and Fittings for Your Manufacturing Operation
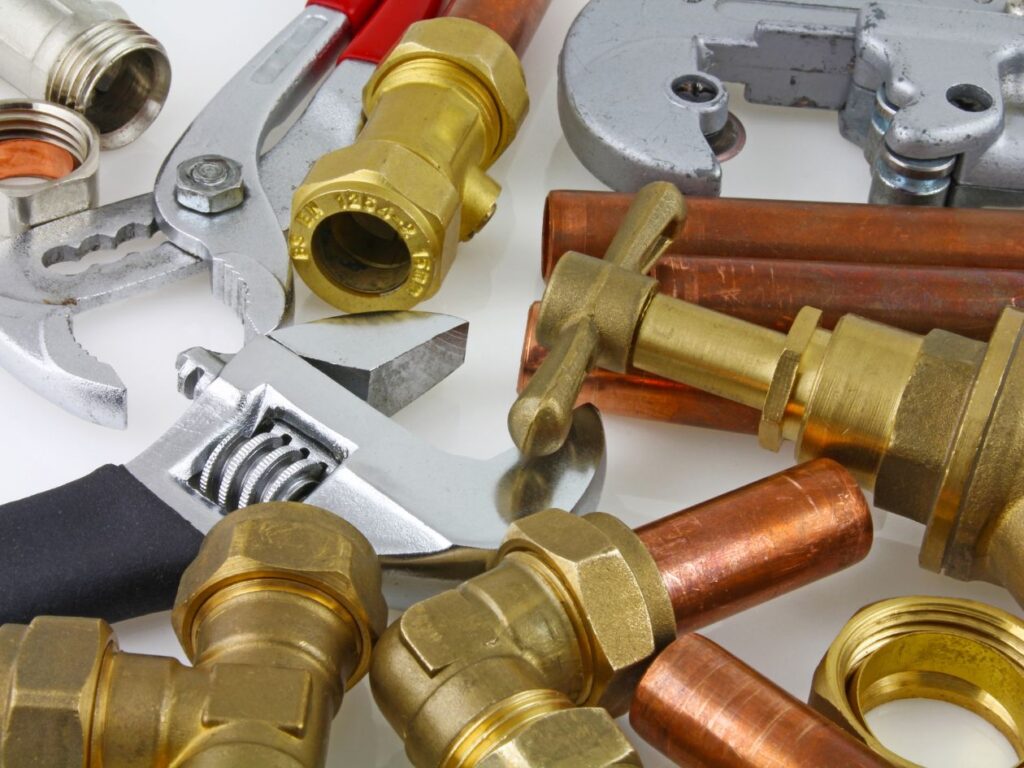
Selecting the right industrial pipes and fittings is one of the most critical decisions in any manufacturing operation. The wrong choice can lead to costly downtime, safety hazards, and expensive repairs. At Cruco Mill & Industrial Supply, we’ve helped manufacturers across North Carolina and beyond make informed decisions about their piping systems for over two decades.
Understanding Your System Requirements
Before diving into specific materials and specifications, it’s essential to understand your system’s unique demands. Manufacturing operations vary significantly in their requirements, and what works for one facility may not be suitable for another.
Pressure Requirements Your system’s operating pressure is the foundation of your piping selection. Consider both normal operating pressure and potential pressure spikes. Always select pipes and fittings rated well above your maximum operating pressure to ensure safety and longevity.
Temperature Considerations Temperature extremes can dramatically affect pipe performance. High temperatures can cause expansion, reduce strength, and accelerate corrosion, while low temperatures can make some materials brittle. Document your system’s temperature range, including seasonal variations and process-specific requirements.
Chemical Compatibility The fluids flowing through your system will interact with your piping materials. Whether you’re handling aggressive chemicals, petroleum products, or simple water systems, understanding chemical compatibility is crucial for preventing premature failure and ensuring worker safety.
Material Selection Guide
Carbon Steel Carbon steel remains the workhorse of industrial piping systems. It offers excellent strength, durability, and cost-effectiveness for most applications. However, it requires proper corrosion protection in wet environments and isn’t suitable for highly corrosive applications.
Stainless Steel When corrosion resistance is paramount, stainless steel is often the best choice. Grades like 304 and 316 offer excellent performance in most industrial environments, with 316 providing superior corrosion resistance for marine or chemical applications.
PVC and CPVC For chemical handling and corrosive environments, PVC and CPVC pipes offer excellent chemical resistance at a lower cost than metal alternatives. They’re lightweight, easy to install, and require minimal maintenance.
Specialized Alloys For extreme environments, specialized alloys like Inconel or Hastelloy may be necessary. These materials come at a premium but provide unmatched performance in the most demanding applications.
Fitting Types and Applications
Threaded Fittings Threaded connections are versatile and easy to install, making them ideal for smaller diameter pipes and applications where disassembly may be required. They’re commonly used in hydraulic systems and instrument connections.
Welded Fittings For permanent, high-pressure applications, welded fittings provide the strongest connection. They’re essential in high-pressure steam systems and critical process lines where leak-free operation is mandatory.
Flanged Connections Flanged fittings allow for easy disassembly and are preferred for larger diameter pipes and equipment connections. They’re standard in pump and valve installations where maintenance access is important.
Compression Fittings These fittings provide a reliable seal without welding or threading, making them perfect for instrumentation and control systems where precision is crucial.
Sizing and Specification Considerations
Flow Rate Requirements Proper sizing ensures optimal flow rates without excessive pressure drop. Undersized pipes create turbulence and increase energy costs, while oversized pipes waste materials and increase installation costs.
Wall Thickness Wall thickness, or schedule rating, determines pressure capacity. Common schedules include Schedule 40 (standard), Schedule 80 (heavy), and Schedule 160 (extra heavy). Higher schedules provide greater pressure capacity but increase material costs.
End Connections Consider how your pipes will connect to existing equipment. Standardizing on common connection types throughout your facility simplifies maintenance and reduces inventory requirements.
Quality Standards and Certifications
ASTM Standards American Society for Testing and Materials (ASTM) standards ensure consistent quality and performance. Common standards include ASTM A53 for carbon steel pipe and ASTM A312 for stainless steel.
ASME Compliance For pressure vessel applications, ASME B31.3 compliance is often required. This standard covers process piping in petroleum refineries, chemical plants, and other industrial facilities.
Industry-Specific Requirements Different industries have specific requirements. Food and beverage operations need FDA-approved materials, while oil and gas facilities require API specifications.
Installation and Maintenance Considerations
Installation Complexity Consider the skill level required for installation. Threaded connections are straightforward, while welded systems require certified welders. Factor installation costs into your total project budget.
Maintenance Requirements Some materials require regular maintenance to maintain performance. Carbon steel may need periodic coating renewal, while stainless steel requires proper cleaning to prevent surface contamination.
Spare Parts Availability Standardizing on common fittings and materials ensures spare parts availability and reduces inventory costs. Consider the long-term availability of specialized components.
Cost Optimization Strategies
Life-Cycle Cost Analysis While initial material costs are important, consider the total cost of ownership. A more expensive stainless steel system may be more economical over its lifetime due to reduced maintenance and replacement costs.
Bulk Purchasing For large projects, bulk purchasing can significantly reduce costs. Work with suppliers like Cruco Mill who offer volume pricing and can coordinate deliveries to match your project timeline.
Standardization Benefits Standardizing on fewer pipe sizes and fitting types reduces inventory complexity and costs while simplifying maintenance procedures.
Common Mistakes to Avoid
Underestimating Pressure Requirements Always account for pressure spikes and system transients. What seems adequate under normal conditions may fail during startup or upset conditions.
Ignoring Thermal Expansion Thermal expansion can generate enormous stresses in piping systems. Proper expansion joints and pipe supports are essential for long-term reliability.
Mixing Incompatible Materials Galvanic corrosion occurs when dissimilar metals are connected in the presence of an electrolyte. Use proper isolation techniques when mixing materials.
Inadequate Support Proper pipe support prevents sagging and stress concentration. Follow industry guidelines for support spacing and load distribution.
Working with Your Industrial Supply Partner
At Cruco Mill & Industrial Supply, we understand that every manufacturing operation is unique. Our team of certified technicians provides comprehensive technical support to help you select the right pipes and fittings for your specific application.
Technical Consultation Our experts can review your specifications and recommend optimal solutions based on your operating conditions, budget, and timeline.
Custom Procurement Services We offer custom procurement services for specialized industrial supplies with competitive lead times and volume pricing options.
Ongoing Support Our relationship doesn’t end with delivery. We provide ongoing technical support and troubleshooting for all products purchased through Cruco Mill.
Choosing the right industrial pipes and fittings requires careful consideration of multiple factors including operating conditions, material properties, installation requirements, and long-term costs. By following this guide and working with experienced industrial supply professionals, you can make informed decisions that optimize your manufacturing operation’s performance, safety, and profitability.
Remember that the lowest initial cost isn’t always the best value. Invest in quality materials and proper installation to minimize downtime and maximize your return on investment. When you’re ready to specify your next piping system, contact the experts at Cruco Mill & Industrial Supply. We’re here to help you keep your industrial business moving.