Sustainable Manufacturing: Green Practices for Today’s Industrial Supply Chain
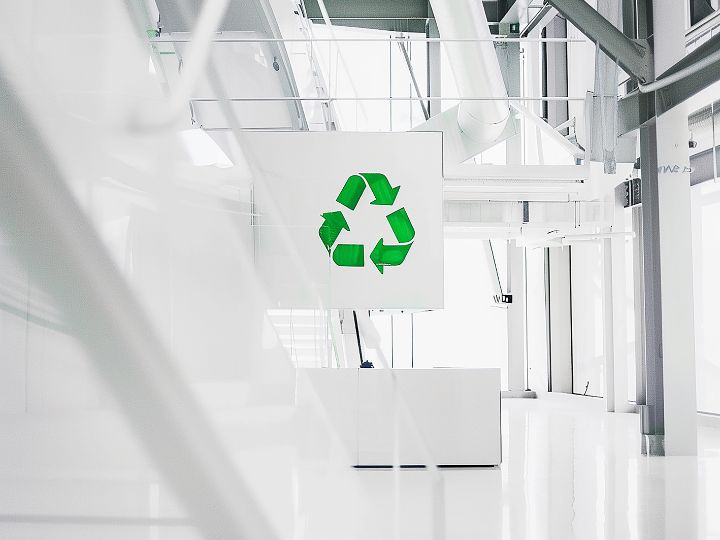
In today’s rapidly evolving industrial landscape, sustainable manufacturing has transformed from a nice-to-have corporate initiative to a fundamental business strategy. As environmental concerns grow alongside regulatory pressures, forward-thinking manufacturers are discovering that green practices not only benefit the planet but also drive innovation, reduce costs, and create significant competitive advantages. This article explores practical approaches to implementing sustainability throughout the industrial supply chain and examines how these practices are reshaping modern manufacturing.
Key Elements of Sustainable Manufacturing
Creating a sustainable manufacturing operation requires a holistic approach that addresses multiple aspects of the business. Here are the core elements that companies should focus on:
1. Energy Management and Carbon Reduction
Energy consumption represents both a significant cost center and a major environmental impact for most manufacturers. Effective energy management includes:
Energy Efficiency Fundamentals
- Comprehensive energy audits and monitoring systems
- High-efficiency equipment upgrades
- Process optimization for reduced energy intensity
- Smart controls and automation for optimal energy usage
Renewable Energy Integration
- On-site solar, wind, or other renewable installations
- Power purchase agreements (PPAs) for clean energy
- Combined heat and power systems
- Battery storage for load balancing
Industrial leader 3M has committed to 100% renewable electricity across global operations, demonstrating how even large manufacturers can transition to cleaner energy sources. Their strategic approach includes a mix of on-site generation, renewable energy certificates, and power purchase agreements tailored to regional energy markets.
2. Materials Selection and Waste Minimization
What goes into products—and what gets left behind as waste—represents another critical sustainability focus:
Sustainable Material Sourcing
- Environmental impact assessment of input materials
- Recycled and renewable content integration
- Bio-based alternatives evaluation
- Low-impact material substitution
Zero Waste Manufacturing
- Waste stream analysis and reduction planning
- Redesign of processes to eliminate waste
- Internal recycling and reuse programs
- By-product synergy with other industries
Toyota’s renowned production system demonstrates how waste reduction principles can transform manufacturing efficiency. By implementing “muda” (waste) elimination strategies, Toyota facilities have achieved up to 95% waste diversion rates while improving productivity and quality.
3. Water Stewardship
Water has emerged as a critical resource requiring careful management:
Water Use Optimization
- Process design to minimize water requirements
- Cooling water recirculation systems
- Leak detection and prevention programs
- Waterless alternatives where possible
Water Recovery and Treatment
- Wastewater recycling and reuse systems
- Advanced treatment technologies
- Rainwater harvesting
- Zero liquid discharge approaches
Unilever’s factories have implemented water efficiency programs that reduced water usage per ton of production by 49% since 2008, showcasing how systematic approaches to water management can deliver remarkable results even in water-intensive manufacturing operations.
4. Supply Chain Sustainability
Truly sustainable manufacturing extends beyond factory walls to encompass the entire supply chain:
Supplier Engagement and Development
- Supplier sustainability assessments and requirements
- Collaborative improvement initiatives
- Capacity building and technical assistance
- Incentives for environmental performance
Logistics Optimization
- Transportation mode selection for reduced emissions
- Route optimization and load consolidation
- Alternative fuel vehicles
- Packaging reduction and optimization
Circular Economy Implementation
- Closed-loop material recovery systems
- Product take-back and remanufacturing programs
- Design for disassembly and recyclability
- Extended producer responsibility initiatives
Apple has shown leadership in this area by transitioning to 100% renewable energy not only for its own operations but also working with suppliers to add 7.8 gigawatts of clean energy to grids worldwide, demonstrating how large manufacturers can leverage their purchasing power to drive sustainability throughout their supply chains.
Implementing Green Practices: A Practical Roadmap
Transforming manufacturing operations for sustainability requires a structured approach that builds momentum while delivering measurable results. Here’s a roadmap for implementation:
1. Assessment and Baseline Development
Begin with a clear understanding of current impacts and performance:
- Environmental footprint analysis to identify hotspots
- Resource consumption mapping across operations
- Waste stream characterization
- Benchmarking against industry standards and competitors
This baseline provides the foundation for improvement planning and allows for meaningful measurement of progress.
2. Strategy Development and Goal Setting
With baseline data in hand, develop a sustainability strategy aligned with business objectives:
- Materiality assessment to identify priority areas
- Science-based target setting for emissions reduction
- Water, waste, and material efficiency goals
- Supply chain engagement strategies
Effective goals are specific, measurable, achievable, relevant, and time-bound (SMART), with both short-term milestones and long-term ambitions.
3. Implementation: Starting with High-Impact Opportunities
Begin implementation with initiatives that deliver rapid results and build momentum:
- Low-hanging fruit with minimal investment requirements
- High-visibility projects that demonstrate commitment
- Quick-win energy efficiency upgrades
- Waste reduction initiatives with immediate ROI
These early successes build credibility for the sustainability program and generate resources for more ambitious projects.
4. Scaling Up: Transformational Initiatives
As the program matures, tackle more substantial opportunities:
- Major capital investments in efficient equipment
- Renewable energy installations
- Process redesign for resource efficiency
- Closed-loop manufacturing systems
- Product redesign for environmental performance
These transformational initiatives often deliver the most significant environmental and financial benefits.
5. Integration into Business Systems
For lasting impact, sustainability must become embedded in core business processes:
- Environmental management systems (such as ISO 14001)
- Design for environment protocols
- Sustainability criteria in capital expenditure approval
- Green procurement policies
- Employee engagement and training programs
This integration ensures that sustainability becomes “the way we do business” rather than a separate initiative.
The Future is Sustainable Manufacturing
Sustainable manufacturing is rapidly becoming the new standard for industrial operations. Companies that embrace this transformation position themselves for long-term success in a resource-constrained, carbon-limited, and increasingly environmentally conscious marketplace.
The business case for sustainable manufacturing has never been stronger. From cost savings and risk management to customer preference and regulatory compliance, green practices deliver tangible benefits while contributing to environmental preservation. As technologies continue to advance and best practices evolve, the opportunities to create value through sustainability will only grow.
For industrial suppliers and manufacturers, the question is no longer whether to embrace sustainable practices, but how quickly and effectively they can implement them. Those who lead this transformation will not only reduce their environmental footprint but also secure competitive advantage in the manufacturing landscape of tomorrow.
Take Your Manufacturing Sustainability to the Next Level with Cruco Mill & Industry Supply
At Cruco Mill & Industry Supply, we’re committed to helping our customers implement sustainable manufacturing practices that benefit both business performance and environmental stewardship. Our comprehensive approach supports your sustainability journey at every stage.
Our Sustainability Solutions include:
- Green Product Portfolio: Environmentally-preferred cutting tools, coolants, lubricants, and supplies that reduce environmental impact without compromising performance.
- Energy-Efficient Equipment: Advanced machinery and tools designed for optimal energy performance and reduced resource consumption.
- Sustainable Process Consultation: Expert assessment of your manufacturing processes to identify sustainability opportunities with rapid returns.
- Tool Reconditioning Programs: Extend tool life and reduce waste through our professional reconditioning services.
- Recycling and Take-Back Programs: Responsible end-of-life management for industrial tools and supplies.
Whether you’re just beginning your sustainability journey or looking to accelerate your environmental performance, Cruco Mill & Industry Supply has the expertise, products, and services to support your goals.Visit https://crucosupply.com/ to learn how we can help you implement sustainable manufacturing practices that benefit your bottom line while protecting our planet.