How to Choose the Right Industrial Cutting Tools for Your Manufacturing Process
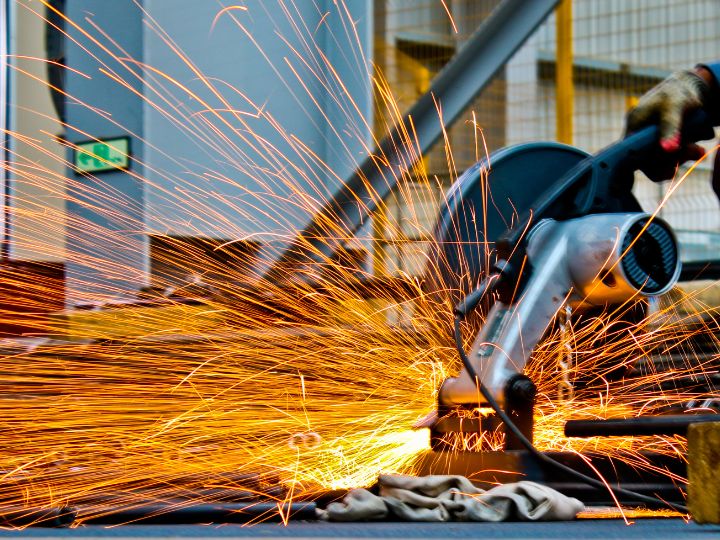
In today’s competitive manufacturing landscape, selecting the right cutting tools isn’t just about making a purchase—it’s about making a strategic investment in your operation’s efficiency, product quality, and bottom line. Whether you’re machining complex aerospace components or fabricating consumer goods, the cutting tools you choose can dramatically impact your production capabilities.
Understanding the Basics: Types of Industrial Cutting Tools
End Mills
End mills are versatile rotating cutting tools primarily used in milling applications. They come in various configurations:
- Flat End Mills: Ideal for creating square shoulders and pockets
- Ball End Mills: Perfect for contoured surfaces and 3D shapes
- Bull Nose End Mills: Combine features of flat and ball end mills, offering strength and versatility
- Roughing End Mills: Designed for rapid material removal with less precision
Drills
Drilling tools create holes and come in several specialized varieties:
- Twist Drills: General-purpose hole creation
- Center Drills: Used to create starter holes for precision drilling
- Spade Drills: For large diameter holes
- Gun Drills: Specialized for deep, precise holes
Turning Tools
For lathe operations, these tools shape materials as they rotate:
- Turning Inserts: Replaceable cutting edges for efficiency and cost-effectiveness
- Boring Bars: For enlarging and finishing internal diameters
- Threading Tools: Create internal and external threads
- Grooving Tools: Form channels and recesses in workpieces
Specialty Cutting Tools
Depending on your industry, you might require:
- Broaches: For precision internal shapes
- Reamers: For hole finishing to tight tolerances
- Gear Cutting Tools: Specialized for gear manufacturing
- Taps and Dies: For creating threaded features
Key Factors in Cutting Tool Selection
1. Material Considerations
The workpiece material is perhaps the most critical factor in tool selection:
For Steels:
- High-speed steel (HSS) tools work for mild steels
- Carbide tools are better for harder steels
- Coated tools extend life when cutting abrasive steel alloys
For Aluminum:
- Polished flutes prevent chip buildup
- Higher helix angles improve chip evacuation
- Diamond-coated tools for high-volume aluminum machining
For Hard Materials (Titanium, Inconel, Hardened Steel):
- Cobalt-enriched tools provide better heat resistance
- Ceramic and cubic boron nitride (CBN) tools handle extreme hardness
- Special geometries designed to reduce cutting forces
For Plastics and Composites:
- Specialized point geometries prevent melting and delamination
- Diamond-coated tools for abrasive composites
- Compression routers for clean edges on laminated materials
2. Operation Type and Precision Requirements
Different operations demand specific tool characteristics:
Roughing Operations:
- Prioritize material removal rate over surface finish
- More flutes generally means smoother finish but slower removal
- Serrated or variable-pitch designs reduce chatter in heavy cuts
Finishing Operations:
- Higher flute counts produce better surface finishes
- More precise tolerances require premium tool grades
- Tool rigidity becomes critical for dimensional accuracy
High-Precision Work:
- Consider specialized micro-machining tools
- Higher-grade carbide substrates maintain edge longer
- Custom geometries may be required for specific features
3. Machine Capabilities and Constraints
Your machine’s specifications directly impact tool selection:
Spindle Speed Limitations:
- Lower RPM machines may require tools designed for lower speeds
- High-speed machines can utilize tools optimized for velocity rather than torque
Rigidity Considerations:
- Less rigid setups require tools that generate lower cutting forces
- Older machines may need more conservative cutting parameters
Tool Holding Systems:
- Match tool shanks to available holders (HSK, CAT, BT, etc.)
- Consider runout characteristics of your holders when selecting precision tools
4. Production Volume and Economics
The economics of cutting tools varies dramatically with production needs:
Low-Volume Production:
- General-purpose tools may be more economical
- Initial investment is typically the primary concern
- Tool life may be less critical than versatility
High-Volume Production:
- Specialized tools optimized for specific operations provide better economy
- Tool life becomes critical to reducing changeover downtime
- Cost per part is more important than initial tool investment
5. Tool Material and Coating Technology
Modern cutting tools offer a range of materials and coatings for optimization:
Tool Materials:
- High-Speed Steel (HSS): Economical for lower-demand applications
- Cobalt HSS: Better heat resistance for tougher materials
- Carbide: Higher hardness and wear resistance
- Ceramic: For extreme hardness materials at high speeds
- Polycrystalline Diamond (PCD): Ultimate performance in non-ferrous materials
- Cubic Boron Nitride (CBN): For hardened steels and superalloys
Coating Technologies:
- Titanium Nitride (TiN): General-purpose coating, gold in color
- Titanium Carbonitride (TiCN): Improved hardness over TiN
- Titanium Aluminum Nitride (TiAlN/AlTiN): Superior heat resistance
- Diamond-Like Carbon (DLC): Excellent for non-ferrous metals
- Zirconium Nitride (ZrN): Good for copper and copper alloys
- Multi-layer coatings: Combine benefits of different coating materials
Common Selection Mistakes to Avoid
1. Over-Prioritizing Initial Cost
One of the most common mistakes is selecting cutting tools based primarily on purchase price. While a less expensive tool may seem like a good deal initially, it often leads to:
- Shorter tool life requiring more frequent replacements
- Reduced cutting parameters limiting productivity
- Lower quality surface finishes requiring additional operations
- Higher scrap rates due to inconsistent performance
Instead, consider the total cost of ownership, including tool changes, downtime, and quality implications.
2. Ignoring Application-Specific Tools
Using general-purpose tools for specialized applications often leads to suboptimal results:
- Standard end mills in hardened materials wear prematurely
- Generic drills in composite materials cause delamination
- All-purpose inserts for exotic alloys produce poor surface finish
For critical operations, application-specific tools almost always provide a better overall economy.
3. Inadequate Tool Management Systems
Even the best cutting tools will underperform without proper management:
- Implement tool life tracking to predict replacements
- Establish consistent setup procedures to maintain repeatability
- Develop a regrinding program for appropriate tool types
- Create a database of optimal cutting parameters for each tool/material combination
Implementation: A Systematic Approach to Tool Selection
To select the optimal cutting tools for your manufacturing process, follow this structured methodology:
Step 1: Analyze Your Requirements
- Document the materials being machined
- Specify required tolerances and surface finishes
- Determine production volumes and timelines
- Identify machine capabilities and limitations
Step 2: Consult Multiple Sources
- Review tool manufacturer recommendations
- Seek input from experienced machinists
- Consider industry benchmarks for similar applications
- Leverage supplier expertise for challenging applications
Step 3: Test and Validate
- Start with recommended cutting parameters
- Document performance metrics (tool life, surface finish, etc.)
- Adjust parameters to optimize performance
- Compare results against production requirements
Step 4: Standardize and Document
- Create a standardized tool selection guide for common operations
- Document optimal cutting parameters for each tool/material combination
- Establish a feedback loop for continuous improvement
- Train operators on proper tool usage and identification
Emerging Trends in Cutting Tool Technology
Stay ahead of the curve by monitoring these developing technologies:
Additive Manufacturing for Cutting Tools
Custom 3D-printed tool bodies with brazed cutting edges are enabling:
- Internal cooling channels impossible with conventional manufacturing
- Weight-optimized designs for higher-speed operation
- Custom geometries tailored to specific applications
Smart Cutting Tools
Integrated sensors in cutting tools and holders are providing:
- Real-time monitoring of cutting forces and vibration
- Predictive tool wear indicators
- Automatic parameter adjustment based on cutting conditions
Hybrid Cutting Technologies
Combining traditional cutting with other processes:
- Laser-assisted machining for hardened materials
- Ultrasonic-assisted cutting for difficult materials
- Cryogenic cooling systems for specialized applications
Selecting the right cutting tools for your manufacturing process requires careful consideration of multiple factors, from workpiece material and machine capabilities to production economics and quality requirements. By taking a systematic approach to tool selection and staying informed about emerging technologies, you can optimize your machining processes for maximum efficiency, quality, and profitability.
Remember that cutting tool selection is not a one-time decision but an ongoing process of refinement and optimization. As materials, technologies, and production requirements evolve, so too should your approach to selecting and utilizing these essential manufacturing components.
Ready to Optimize Your Manufacturing Process? Contact Cruco Mill & Industry Supply Today!
At Cruco Mill & Industry Supply, we understand that choosing the right cutting tools can be challenging. That’s why our team of experienced technical specialists is ready to help you select the optimal tools for your specific applications.
Our comprehensive services include:
- Free cutting tool consultations and application reviews
- Access to premium brands and specialized cutting tools
- Custom tool grinding and modification services
- Tool management programs to reduce your inventory costs
- Technical training for your machining team
Don’t waste time and money on trial-and-error approaches to tool selection. Contact Cruco Mill & Industry Supply today for expert guidance and superior products that will take your manufacturing capabilities to the next level.Visit https://crucosupply.com/ to schedule your consultation. Your perfect cutting tool solution is just a click away!